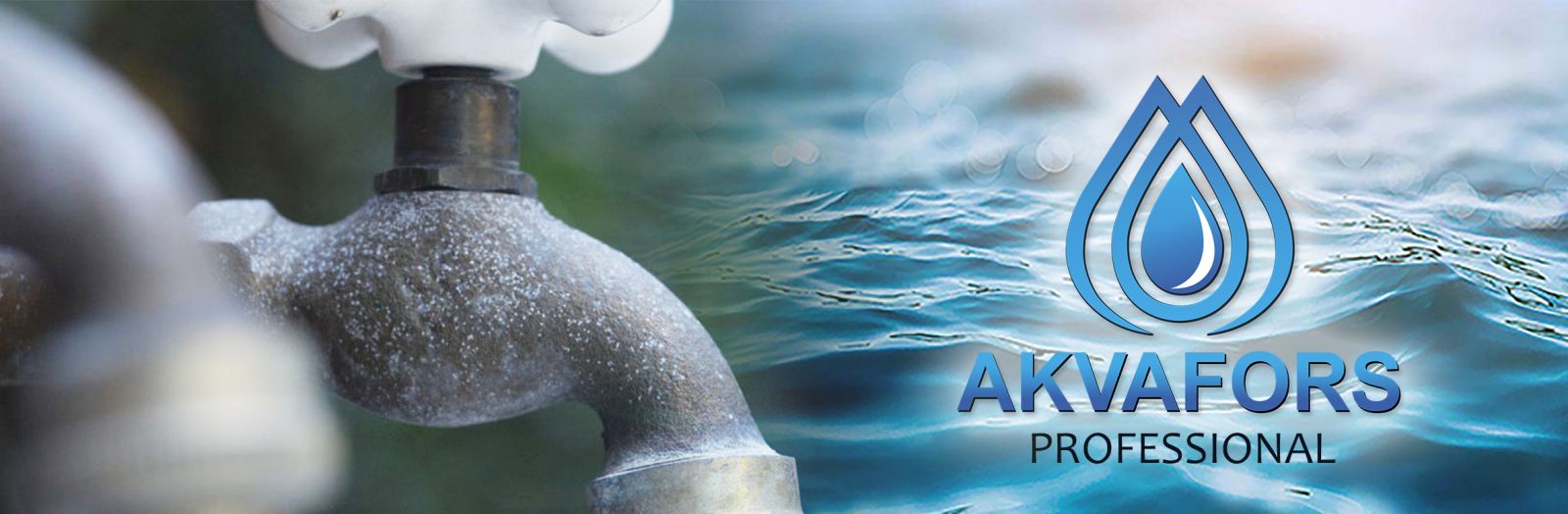
Purpose:
Removal of dissolved iron, manganese and hydrogen sulfide from water.
Areas of use:
Enterprises of food, metallurgical, petrochemical, perfumery and other industries, boiler houses and other housing and communal services facilities, water preparation for reverse osmosis treatment.
Filter material:
Manganese Greensand (MGS) natural glauconite coated with manganese oxide MnO2 or MTM filter material in the form of light granules coated with manganese oxide MnO2.
Anthracite - for filtering solid and suspended particles and protecting MGS and MTM from contamination.
Job management:
automatic:
using an electromechanical or electronic control mechanism for the volume of treated water (counter) or at regular intervals (timer).
manual:
using a mechanical control mechanism by the volume of treated water or at regular intervals (determined by the operator).
Oxidizing filters (or iron removal filters)
System complete set:
- filter column (material - fiberglass reinforced with food-grade inner surface, no seams);
- loading (filter material, gravel);
- distribution system;
- control mechanism;
- potassium permanganate tank.
Reagent removal of dissolved iron, manganese and hydrogen sulfide from water occurs in pressure filter columns.
Usually MGS or MTM is used as filter material. Manganese oxide is an oxidizing agent for iron, manganese and hydrogen sulfide. Iron removal and / or demanganation processes are processes that lead to the fact that iron or manganese dissolved in water transforms into an insoluble form and precipitates.
During the operation of the system, the catalytic activity of the filter material decreases. To restore it, automatic or manual regeneration is carried out using a solution of potassium permanganate (KMnO4).
Regeneration (restoration of catalytic activity) includes five stages:
- backwash (backwash),
- passing the potassium permanganate solution through MGS or MTM (brine draw),
- slow rinse (slow rinse),
- fast rinse (rapid rinse),
- filling the potassium permanganate tank with water (brine tank refill).
Service flow - depending on the technical task.
Execution options:
T - automatic (timer) regeneration control
Feed - automatic (counter) regeneration control
Mn - manual regeneration control
NBP - built-in valve to prevent dirty water from entering the consumer during system regeneration
EM - automatic (electronic counter and timer) regeneration control
Guaranteed water quality after treatment with the KAMG series system:
- manganese - no more than 0.1 mg / l
- total iron - no more than 0.3 mg / l
- lack of microbiological contamination;
- pH 6.2 - 8.5;
- lack of oil products;
- lack of polyphosphates;
- maximum concentration of hydrogen sulfide in the treated water - 5 mg / l
- the maximum concentration of reduced iron (total concentration of iron ions, manganese and hydrogen sulfide) - 15 mg / l;
- treated water temperature - up to 26.7 ° С;
- the maximum size of solid particles is no more than 50 microns.
- working pressure - from 2.1 to 8.6 atm.
- electrical parameters of the control mechanism - 220 V, 50 Hz, 25 W.
- indoor air temperature 5 - 35 ° С, humidity - no more than 70%;
- the presence of a drainage system.